
These are designed to retain lubricant, for sliding and bearing type applications.Ĭhrome plating is used for wear and corrosion resistance in addition to its tribological (low friction) characteristics. Porous chrome plating is developed by etching electrodeposited chromium. The formation of micro-porous chromium is achieved by a specialised plating method involving the use of inert suspended particles. Micro-cracked chromium has a Vickers hardness of 800-1000 kg/mm2, while crack-free chromium has Vickers hardness between 425-700 kg/mm2. It is essential that the micro-cracked and porous coatings have a minimum thickness between 80-120µm in order to confer adequate corrosion resistance. Various types of hard chrome include micro-cracked chromium, micro-porous chromium, porous chromium and crack free chromium. Thickness of hard chrome plating ranges from 2 to 250µm. Hard chrome plating is an electroplating process in which chromium is deposited from a chromic acid solution. Hard Chrome Plating ( Industrial hard Chrome ) : Hard chrome plating is commonly applied to various types of steel and is almost always thicker than decorative chrome plating.
/Chrome-vs-Chromium-94e4a3896cb7455386b29982db41625f.jpg)
Hard chrome plating, while it can improve the corrosion resistance of the material to which it is applied, is primarily used to increase the wear resistance of certain components. This type is typically used in industrial settings where aesthetic appeal is not the primary concern. Decorative chrome plating usually has a total thickness under 0.001 inch. The chromium layer helps increase the corrosion resistance of the material and also improve the resistance to scratching and wear. Once the nickel layer has been deposited, a chromium layer is added on top of it. The nickel gives the surface of the object its shine and its polished look. This type employs a layer of nickel and a layer of chromium. There are two main types of chrome plating: Sometimes the component enters the chrome plating vat while electrically live. Ferric chloride is also popular for the etching of nimonic alloys. Different substrates need different etching solutions, such as hydrochloric, hydrofluoric, and sulfuric acids.
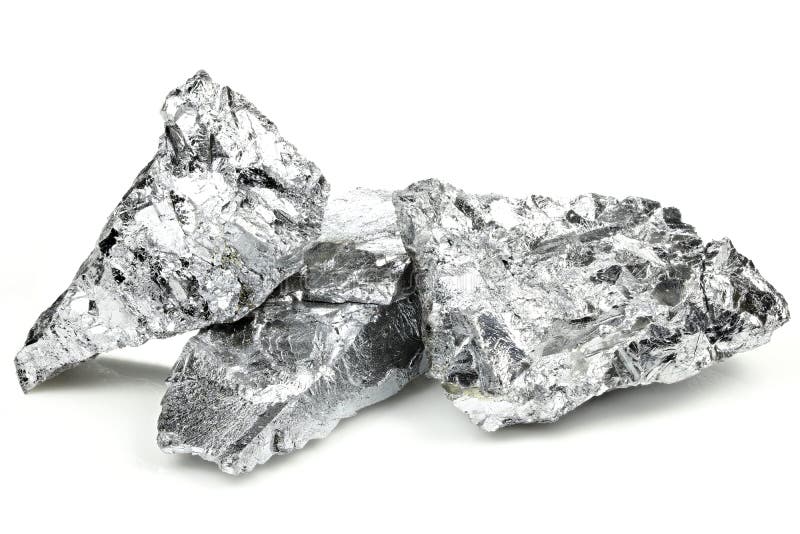
Application of plating current for the required time to attain the desired thickness.Placement into the chrome plating vat, where it is allowed to warm to solution temperature.Various pretreatments depending on the substrate.Manual cleaning to remove all residual traces of dirt and surface impurities.Chrome plating a component typically includes these stages:
